Die Automatisierung schreitet mit einem hohen Tempo voran und fördert und entwickelt eine große Vielfalt an Optionen. Auch im Bereich der industriellen Robotik hat die technologische Entwicklung im letzten Jahrzehnt rasant zugenommen. Dabei geht es verstärkt um intelligente Komponenten, Plug & Play Schnittstellen, Cloud Computing sowie kundenfreundliche Benutzung. Roboter gibt es in vielen Formen. Die einzelnen Industrieroboter sind auf bestimmte Arbeitsgebiete spezialisiert. Dabei werden u. a. hohe Traglasten mit einer enormen Geschwindigkeit bewegt. Damit der Mensch nicht zu Schaden kommt, erfordern diese Roboter einen Schutzzaun. Inzwischen gibt es aber Mischformen oder Allrounder, die eine Arbeit gemeinsam mit dem Menschen erlauben. Hier spricht man von sog. Cobots (kollaborierende Roboter). Aufgrund der Sicherheitseinstufung und der Einhaltung der Maschinenrichtlinien und Normen sind die jedoch deutlich langsamer, um Menschen nicht zu gefährden. Eine Gegenüberstellung der traditionellen Industrieroboter und den neuen Allroundern bietet die Grafik.
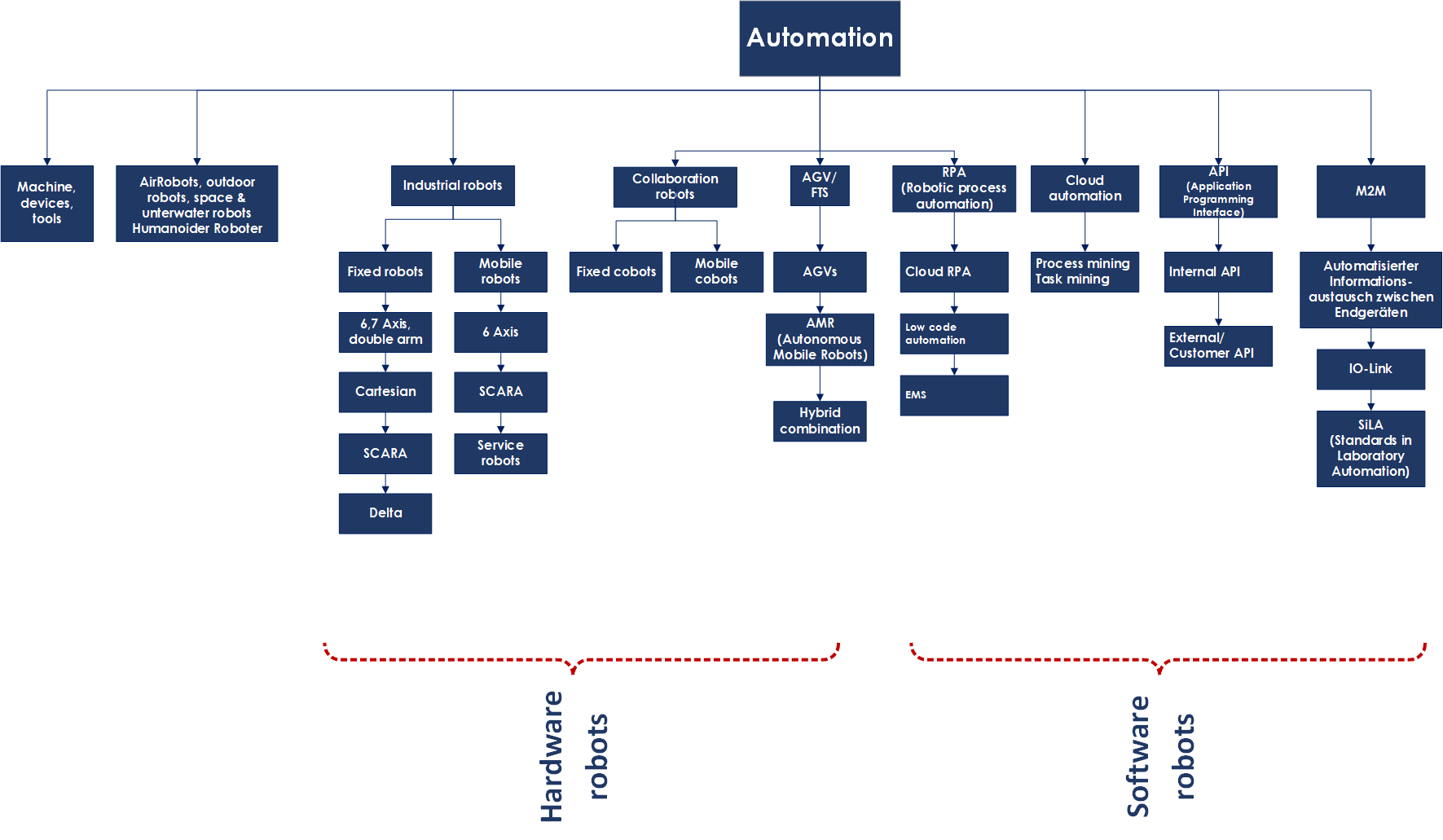
Die Digitalisierung schreitet unaufhörlich voran. Mancherorts klingt das eher nach Zukunftsmusik, aber wir befinden uns mittendrin. Für einen erfolgreichen digitalen Wandel ist eine systematische und ganzheitliche Betrachtung von großer Bedeutung. Auch im Toyota Haus ist die Rede von Jidoka. Die rechte, technologische Säule, dargestellt als das TPS Haus, schließt Methoden ein, die zur Vermeidung von Verschwendung in den Produktionsprozessen beitragen sollen. Dazu gehören nicht nur eine kontinuierliche Verbesserung, sondern auch eine intelligente Automatisierung (Jidoka). Jedoch ist es so dass Automatisierung nicht gleich Automatisierung ist. Das Spektrum ist inzwischen sehr breit gefächert. Auch bei Lean Automation gilt der Grundsatz „simplify first, automate afterwards“. Das Ziel dabei ist:
● Nicht zu komplexe und langwierige Umsetzung
● Einfache Umsetzung und benutzerfreundlich
● Niedrige Investitionskosten
● Nicht zu komplexe und langwierige Umsetzung
● Einfache Umsetzung und benutzerfreundlich
● Niedrige Investitionskosten
Umsetzung
Weltweit gibt es ein paar große Player, um diese herum hat sich ein ganzer Industriezweig mit sehr unterschiedlichen Lösungsansätzen entwickelt. Die Autoindustrie hat früh mit der Automatisierung begonnen und zeigt heute innerhalb Ihrer Hallen ganze Roboterstraßen. Sie sind auch die größten Abnehmer für Industrieroboter. Nun ist es jedoch so dass in den meisten Industriebereichen die Mehrheit der wertschöpfenden oder auch nicht-wertschöpfender Tätigkeiten nicht automatisiert sind. Die größte Hürde hierzu sind nach wie vor die hohen Anschaffungskosten. Selbst ein relativ einfacher Industrieroboter, der in eine bestehende Linie integriert werden soll, liegt preislich bei 130.000 bis 250.000 Euro. Der Grund dafür sind nicht nur die hohen Anschaffungskosten, sondern auch die komplexe Integration. Für die zeitliche Umsetzung, angefangen von der Suche nach einem Lieferanten bis hin zur finalen Abnahme, können 10 bis 14 Monate vergehen. (Lieferantengespräche, Lieferantenauswahl, Engineering, Komponentenbestellung, Programmierung, Dokumentenerstellung usw.). Hinzu kommt, dass nicht jedes Unternehmen das Know how besitzt, um solche Projekte voranzutreiben. Viele mittelständische Unternehmen haben keinen eigenen Programmierer. Auch die Programmierung der Roboter ist je nach Hersteller unterschiedlich. Größere Unternehmen verfügen zwar über das Wissen, die Herausforderung liegt jedoch darin, wie solche Projekte dann lokal an anderen Standorten umgesetzt werden können. Natürlich gibt es auch Dienstleister, die solche Projekte umsetzen. Dennoch bleibt die interne Projektdurchführung eine große Herausforderung.
Der Grundgedanke des Lean Thinking ist die gezielte Ausrichtung aller Prozesse eines Unternehmens auf die Wertschöpfung für den Kunden. Dabei lassen sich die Prinzipien des Lean Thinking auch auf die Thematik der Automation übertragen. Bei der Lean Automation bewegen wir uns auf der Prozessebene. Somit ist hier zu unterscheiden wer der interne Lieferant (Abteilung A) und wer der interne Kunde (Abteilung B) ist. Die Aufnahme des IST-Zustands erfolgt anhand der Wertstrommethode (der Einsatz von Makigami wäre ebenfalls möglich). Auch hier ist es sehr wichtig zunächst das Problem genau zu verstehen und klar zu definieren, bevor Lösungen gesucht werden. In diesem Zusammenhang soll dann die manuelle Tätigkeit, die es gilt zu untersuchen, genau erfasst werden. Welche Aufgaben wiederholen sich? In welcher Frequenz? Gibt es Zahlen, Daten, Fakten dazu. Der IST-Zustand umfasst all die manuellen Tätigkeiten und der SOLL-Zustand beschreibt die umgesetzten Aufgaben durch den Roboter. Im nächsten Schritt werden die Zustände miteinander verglichen und untersucht, wo es einen „Gap“ gibt. Danach geht es darum diese Lücken zu schließen. Je näher am SOLL-Zustand desto besser ist es. Die Abbildung reflektiert eine zweckmäßige Abbildung auf unterschiedlichen Ebenen.
Praktische Vorgehensweise:
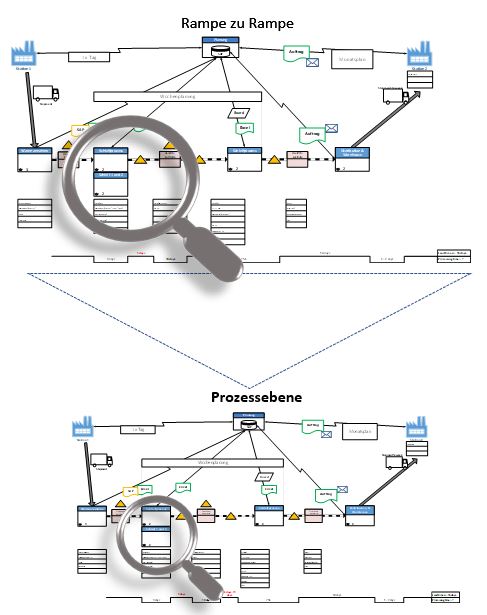
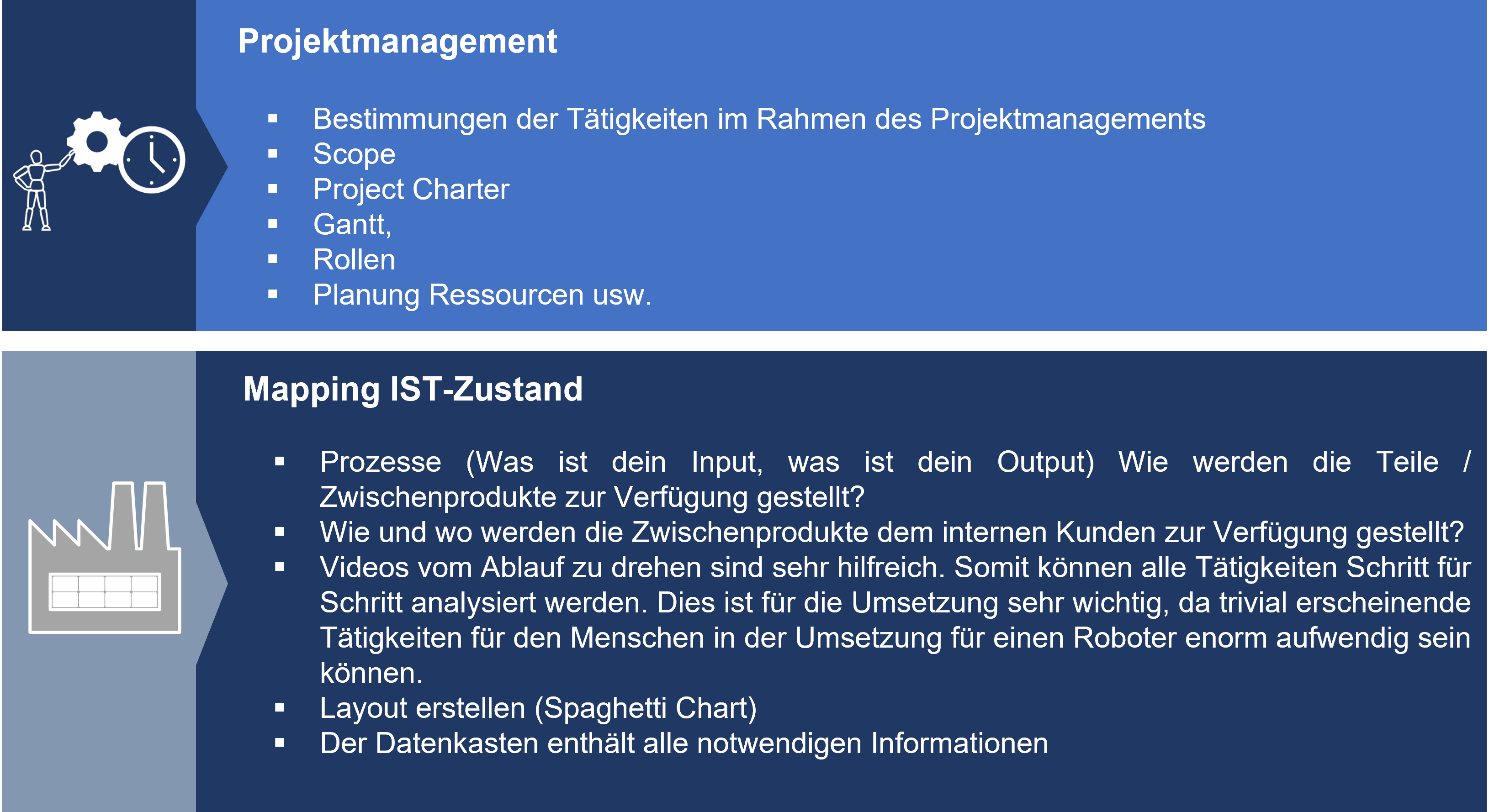
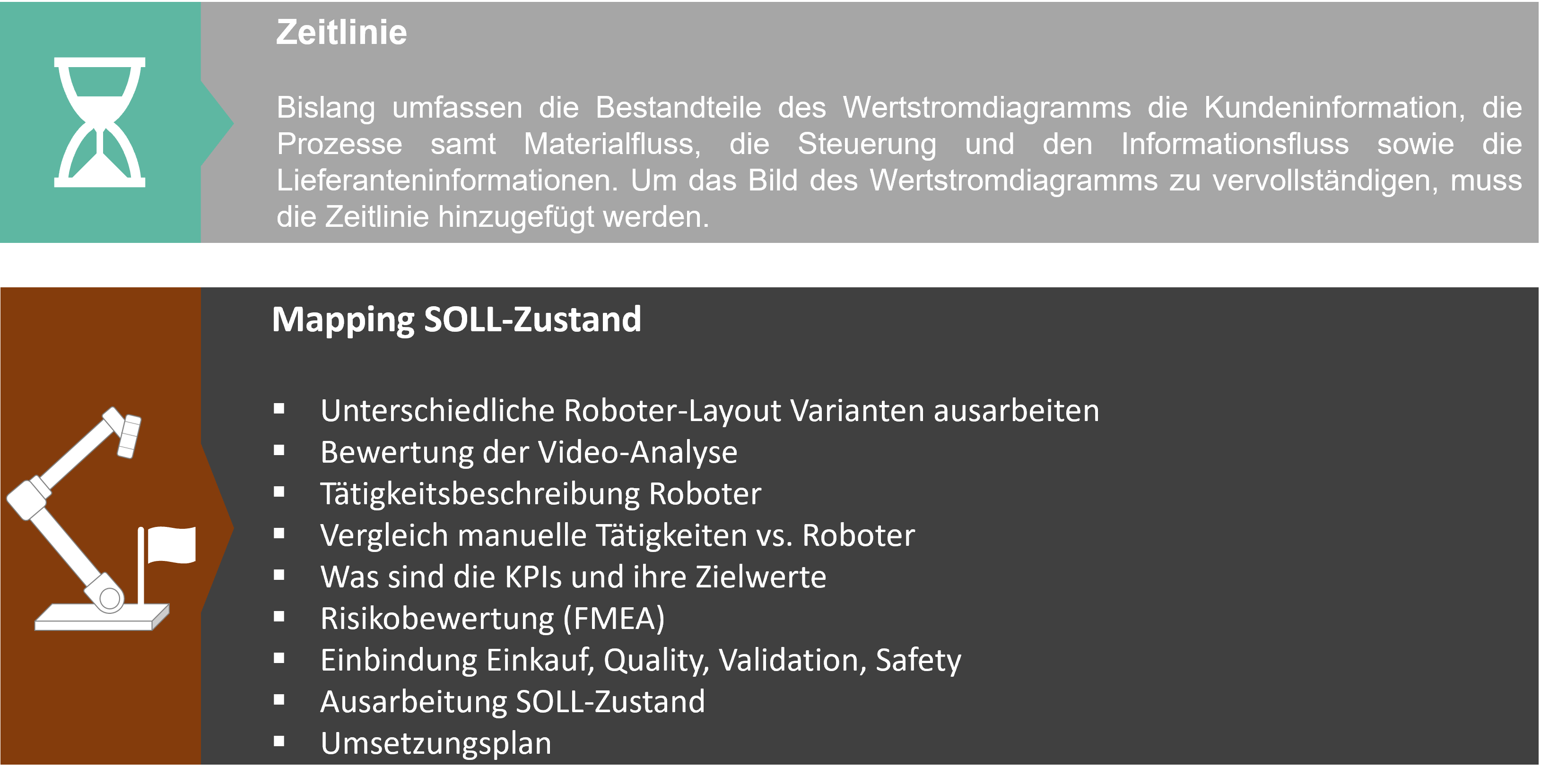
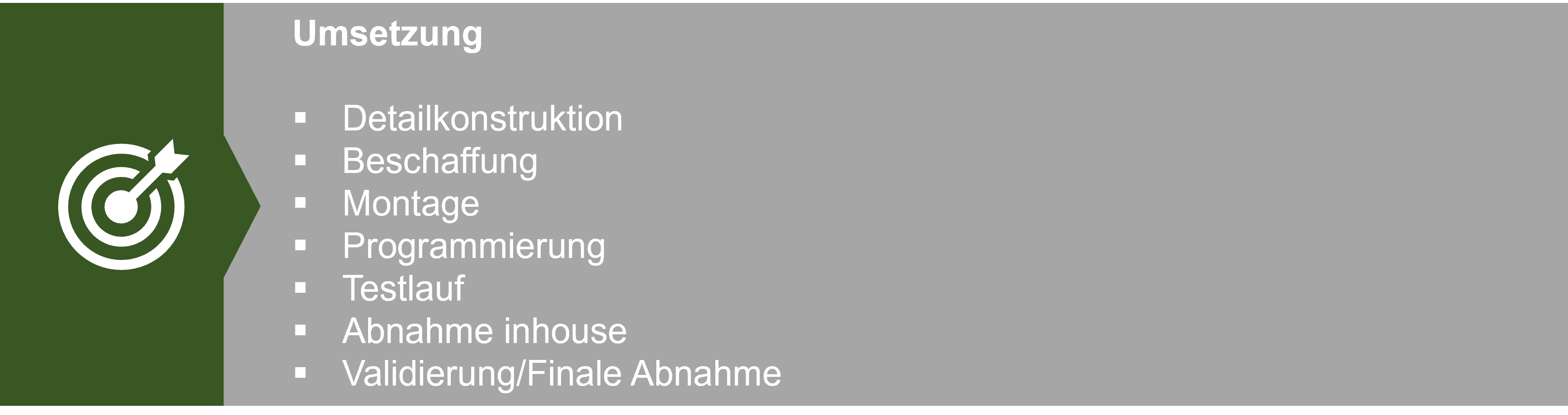
FTS/AGV
Im Bereich der fahrerlosen Transportsysteme (FTS) hat sich sehr vieles getan. Neue Möglichkeiten drängen auf den Markt. Die Installation von FTS ist in den letzten Jahren deutlich gestiegen. Im englischen Sprachraum spricht man von AGV (Automated Guided Vehicles).
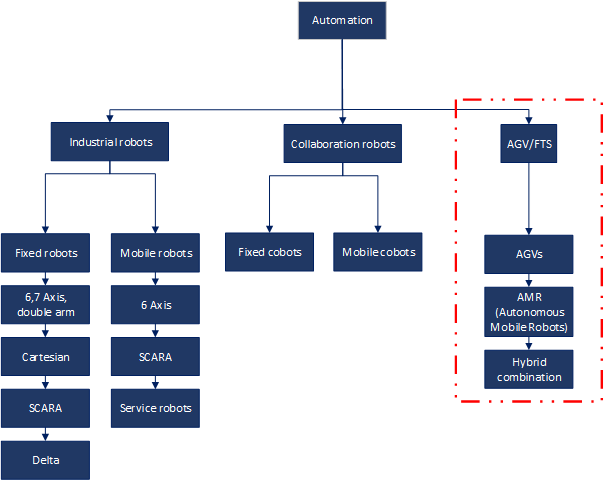
FTS haben eine minimale Bordintelligenz und können nur einfache Programmieranweisungen umsetzen. Die Navigation erfolgt entweder durch Magnetstreifen, Drähten oder Sensoren. Die Installation ist in der Regel umfangreicher, da unter Umständen die Produktion unterbrochen werden muss. FTS sind auf festen Routen begrenzt. Je Änderung kann zusätzliche Kosten und Unterbrechungen verursachen. Jedoch können FTS sowohl im Indoor als auch im Outdoor-Bereich eingesetzt werden. Auch eine Kombination zwischen Indoor und Outdoor ist möglich.

AMR
AMRs sind kollaborativ und darauf ausgelegt, mit Menschen zusammenzuarbeiten. Im Gegensatz zu FTS navigiert das AMR über Karten, die seine Software vor Ort erstellt, oder über vorinstallierte Anlagenzeichnungen. Diese Funktion kann mit einem Auto mit GPS und einem vorinstallierten Kartensatz verglichen werden. Sobald die Ausgangssituation sowie die Abhol- und Lieferstation den AMRs beigebracht wird, generiert er den kürzesten Weg auf Basis der Positionen auf der Karte. Der AMR verwendet Daten von Kameras und eingebauten Sensoren und Laserscannern sowie eine ausgeklügelte Software, die es ihm ermöglicht, seine Umgebung zu erkennen und effiziente Routen zum Ziel zu bestimmen. Es arbeitet völlig autonom und wenn Gabelstapler, Paletten, Personen oder andere Hindernisse vor ihm auftauchen, umfährt das AMR diese sicher auf der besten Alternativroute. Dies verbessert die Produktivität, indem sichergestellt wird, dass der Materialfluss im Zeitplan bleibt. Die Grafik zeigt die unterschiedlichen Navigationstypen in Kombination mit der Kostenentwicklung.
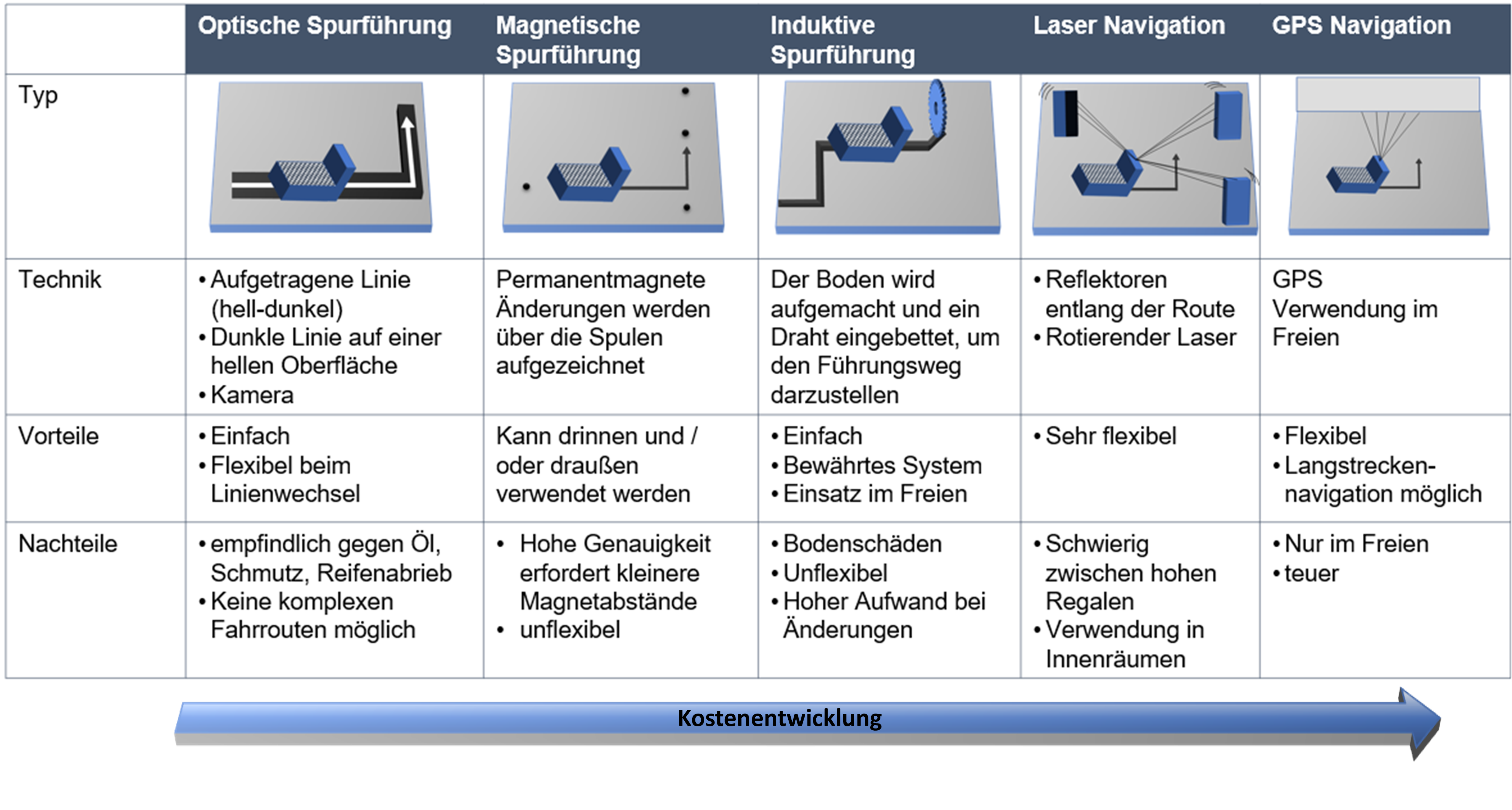